DFA (Design for Assembly) 10 日本語版 - 製品簡略化ツール
概要
1982年から世界で850ユーザに利用されてきたDFA(Design for Assembly) ソフトウェアバージョン10日本語版がリリースされました。
+++ DFAツールの特長 +++
* 理論最少部品基準による部品数削減
* 組立時間の算出データベース
* 組立性評価指数 (DFA指数)による組立性評価
DFMAはロードアイランド大学のブースロイド博士とデュウハースト博士により開発された手法で「組立が容易な製品設計は部品数が最少になる」という理論に基づいています。 DFMA理論の最大の成果の一つは、理論最少部品数を定義したことです。 以下の質問のいずれかに該当すると、その部品は削減できない必要部品と判定されます。 その他の全ての部品は理論上、削除可能か、もしくは必要部品と一体化できると考えられます。
1. その部品は、他の部品に対し相対的に動く必要がある? >> 例:シリンダー内のピストン
2. その部品は、他の部品と異なる材料にしなければなりませんか? >> 例:ケーブルのコネクタ 、センサ
3. その部品は、組立や分解のために他の部品と分けておく必要性がある? >> 例:電池などを交換するため蓋、部品のカバー
もし、上記の基準のいずれにも該当しないのに、設計上、別部品とする必要がある場合には、設計者は「なぜ別部品にする必要があるか」その理由の説明が求められます。 このようにして、DFA手法により、部品の一体化を進めることにより部品点数を最少化し、組立コストの低減が可能になります。
「理想的な」製品とは理論最少部品で構成される製品を指します。 この理想の製品に対する現行製品の組立性を示す評価基準であるDFA指数は、自社製品の設計の良し悪し(組立のしやすさ)を評価する指標として利用することができます。
DFA10では、ユーザが部品数低減のための分析と製品再設計に集中できるよう、ソフトウェアのユーザインターフェースが刷新されました。 製品コストの8割は図面の内容で決まるといわれています。DFAは 「組立が容易なように製品を設計することが設計者の総合目標であるべき」であるという考えのもと、生産が容易な設計を研究してきた成果です。
+++ DFAツールの特長 +++
* 理論最少部品基準による部品数削減
* 組立時間の算出データベース
* 組立性評価指数 (DFA指数)による組立性評価
DFMAはロードアイランド大学のブースロイド博士とデュウハースト博士により開発された手法で「組立が容易な製品設計は部品数が最少になる」という理論に基づいています。 DFMA理論の最大の成果の一つは、理論最少部品数を定義したことです。 以下の質問のいずれかに該当すると、その部品は削減できない必要部品と判定されます。 その他の全ての部品は理論上、削除可能か、もしくは必要部品と一体化できると考えられます。
1. その部品は、他の部品に対し相対的に動く必要がある? >> 例:シリンダー内のピストン
2. その部品は、他の部品と異なる材料にしなければなりませんか? >> 例:ケーブルのコネクタ 、センサ
3. その部品は、組立や分解のために他の部品と分けておく必要性がある? >> 例:電池などを交換するため蓋、部品のカバー
もし、上記の基準のいずれにも該当しないのに、設計上、別部品とする必要がある場合には、設計者は「なぜ別部品にする必要があるか」その理由の説明が求められます。 このようにして、DFA手法により、部品の一体化を進めることにより部品点数を最少化し、組立コストの低減が可能になります。
「理想的な」製品とは理論最少部品で構成される製品を指します。 この理想の製品に対する現行製品の組立性を示す評価基準であるDFA指数は、自社製品の設計の良し悪し(組立のしやすさ)を評価する指標として利用することができます。
DFA10では、ユーザが部品数低減のための分析と製品再設計に集中できるよう、ソフトウェアのユーザインターフェースが刷新されました。 製品コストの8割は図面の内容で決まるといわれています。DFAは 「組立が容易なように製品を設計することが設計者の総合目標であるべき」であるという考えのもと、生産が容易な設計を研究してきた成果です。
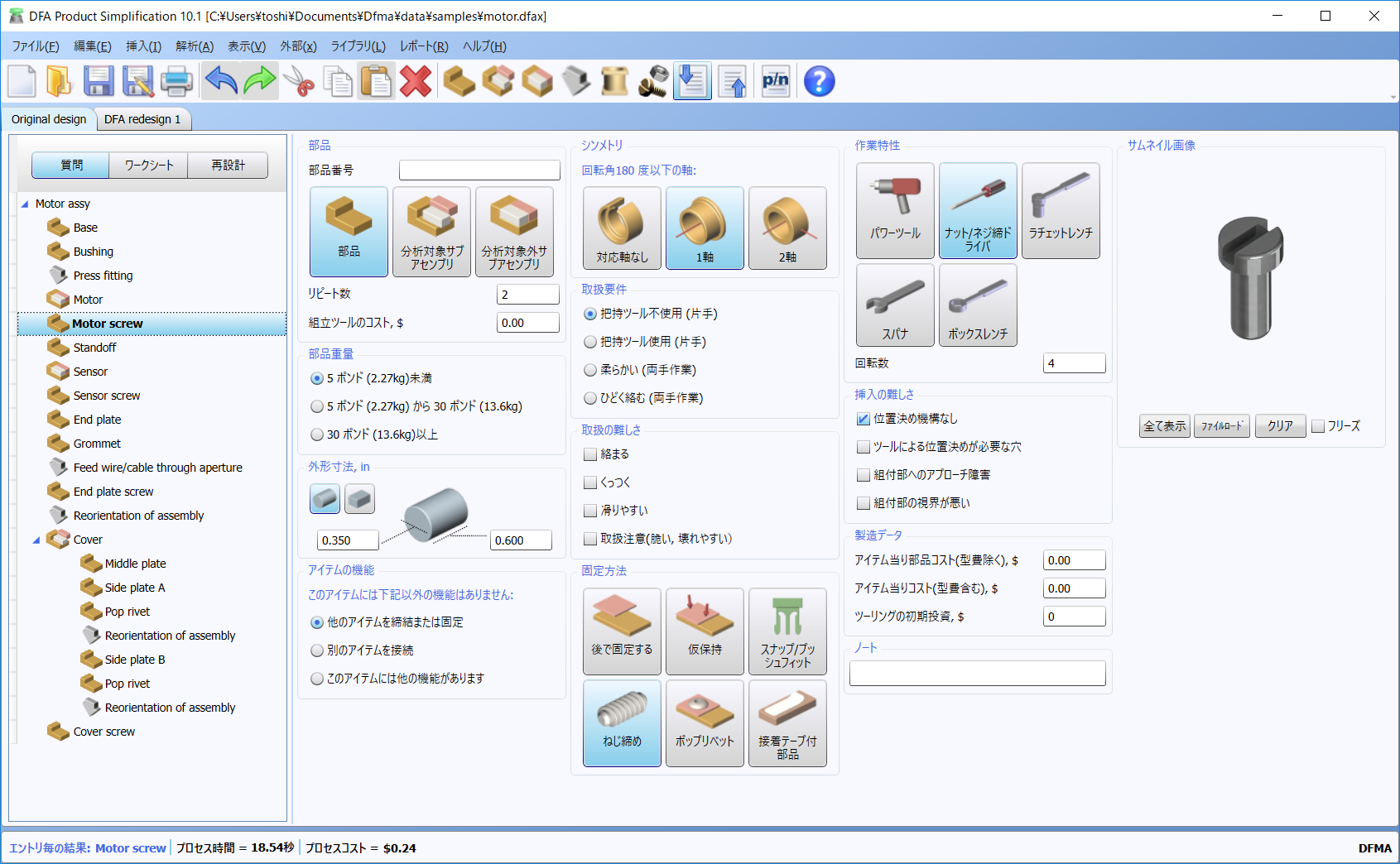
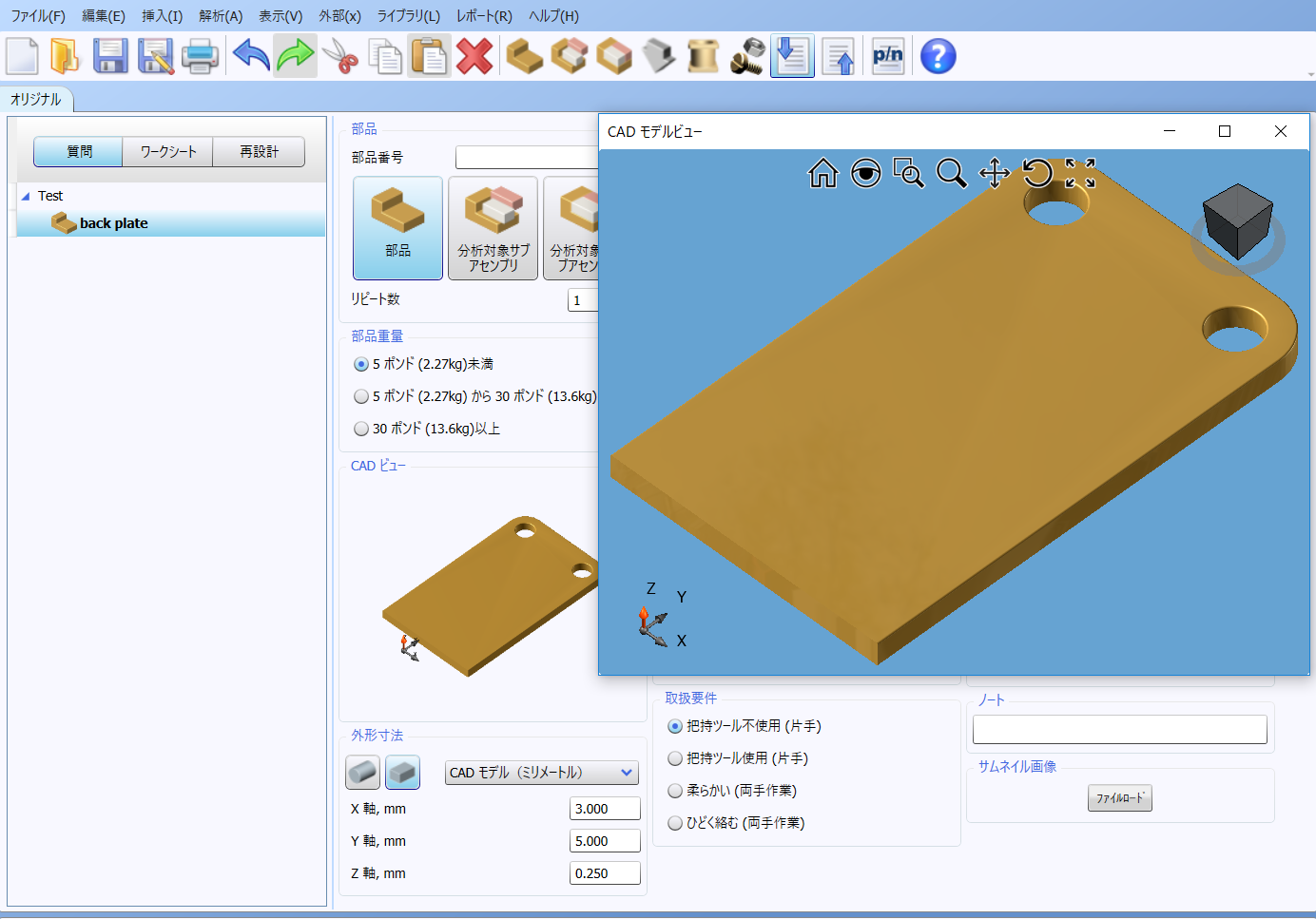
動画
特徴
DFA 10の新機能
1) 組立方法と部品の取扱いに関し、最も重要なDFA 質問にのみ答えるだけで分析ができるようになりました。
2) CADデータと部品表のインポートが容易になりました。
3) 表組カスタムレポートの作成、複数レポートの一括印刷
ソフトウェアの基本コンセプトはそのままに、ユーザの利便性を向上しました。
詳細は以下のサイトをご覧ください。
https://www.imprimis.jp/dfa-version10.html
DFAツールは、非常に簡単な以下のステップで使用できます。
1) 部品表作成
2) 部品間の締結方法、形状、取り扱いの難しさ等の質問に対話形式で答えることにより、その製品の組立時間が算定されます。
3) 同時に、製品の組立てやすさの指標となるDFA指数も計算されます。DFA指数は、旧製品と新製品の組立性の改善度の評価や製品の設計指標として利用することができます。
4) 再設計のための提案レポート(下図)を検討することにより、部品数を最小限に押さえ、実際の生産時の作業時間、部品管理、納品コストが削減できます。 削減の対象となる問題部品をリストアップし、部品をなくすことで削減可能な時間と合計組⽴時間に与える影響(%)を表示しています。
1) 組立方法と部品の取扱いに関し、最も重要なDFA 質問にのみ答えるだけで分析ができるようになりました。
2) CADデータと部品表のインポートが容易になりました。
3) 表組カスタムレポートの作成、複数レポートの一括印刷
ソフトウェアの基本コンセプトはそのままに、ユーザの利便性を向上しました。
詳細は以下のサイトをご覧ください。
https://www.imprimis.jp/dfa-version10.html
DFAツールは、非常に簡単な以下のステップで使用できます。
1) 部品表作成
2) 部品間の締結方法、形状、取り扱いの難しさ等の質問に対話形式で答えることにより、その製品の組立時間が算定されます。
3) 同時に、製品の組立てやすさの指標となるDFA指数も計算されます。DFA指数は、旧製品と新製品の組立性の改善度の評価や製品の設計指標として利用することができます。
4) 再設計のための提案レポート(下図)を検討することにより、部品数を最小限に押さえ、実際の生産時の作業時間、部品管理、納品コストが削減できます。 削減の対象となる問題部品をリストアップし、部品をなくすことで削減可能な時間と合計組⽴時間に与える影響(%)を表示しています。
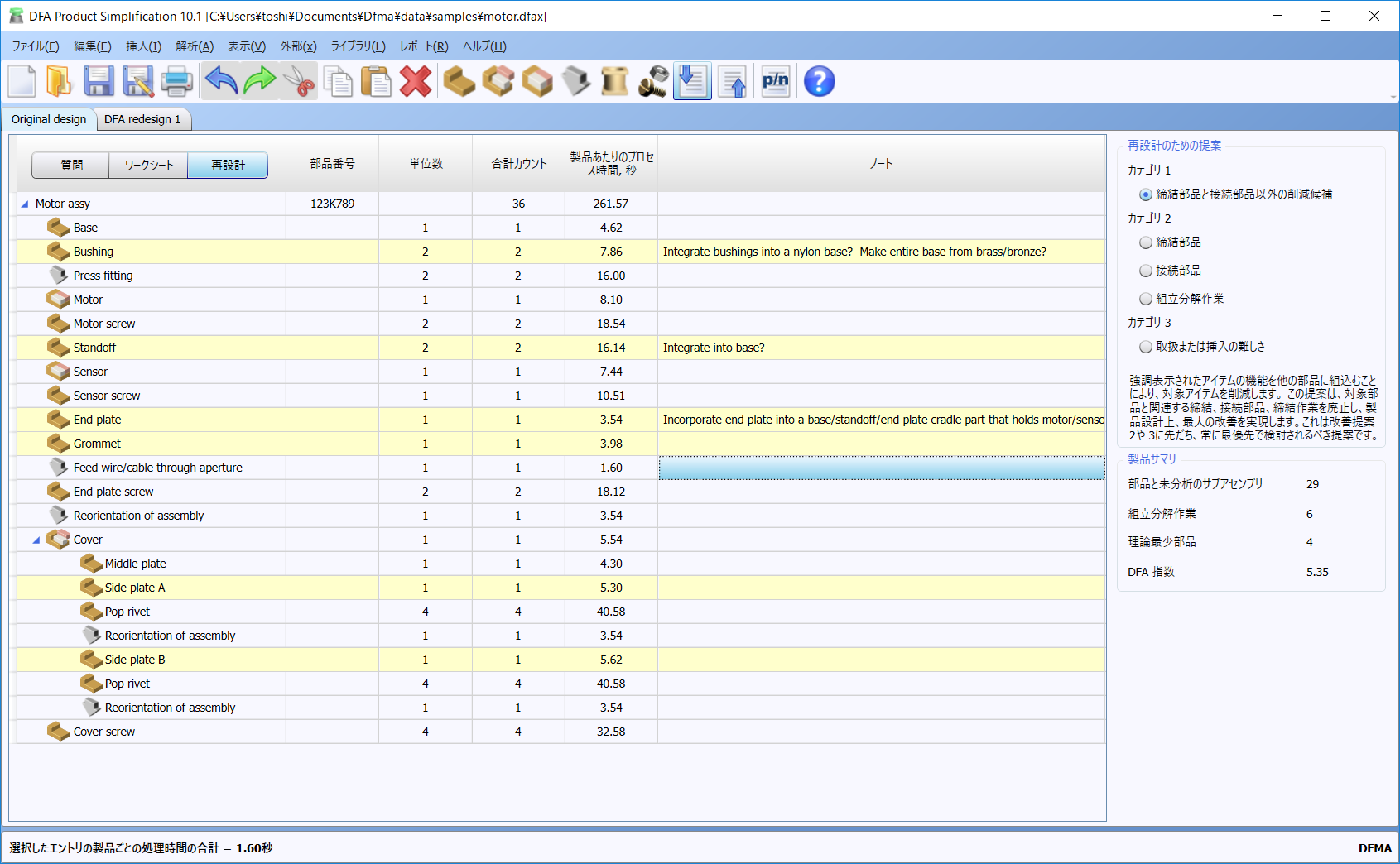
製品URL
用途・実績
◆用途
全ての組立製品のコスト低減。 旧製品に対する新製品の改善度評価には最適です。
◆実績
1983年Boothroyd Dewhurst社設立以来、DFMA は自動車業界を中心に世界850の企業で採用され、製造業における基本コンセプトの一つになっています。
1991年には米国製造業の復権に貢献したとして当時のブッシュ大統領より National Medal of Technology (アメリカ国家技術賞) を受賞しています。
* アメリカ国家技術賞は、革新的で重要な技術の開発に多大な貢献をした発明家に対してアメリカ合衆国大統領から授与される賞で、技術分野ではアメリカ合衆国で最高の栄誉とされています。 受賞者には、スティーブ・ジョブズとスティーブ・ウォズニアック、ゴードン・ムーア、ビル・ゲイツ、ベル研究所などが含まれています。)
全ての組立製品のコスト低減。 旧製品に対する新製品の改善度評価には最適です。
◆実績
1983年Boothroyd Dewhurst社設立以来、DFMA は自動車業界を中心に世界850の企業で採用され、製造業における基本コンセプトの一つになっています。
1991年には米国製造業の復権に貢献したとして当時のブッシュ大統領より National Medal of Technology (アメリカ国家技術賞) を受賞しています。
* アメリカ国家技術賞は、革新的で重要な技術の開発に多大な貢献をした発明家に対してアメリカ合衆国大統領から授与される賞で、技術分野ではアメリカ合衆国で最高の栄誉とされています。 受賞者には、スティーブ・ジョブズとスティーブ・ウォズニアック、ゴードン・ムーア、ビル・ゲイツ、ベル研究所などが含まれています。)
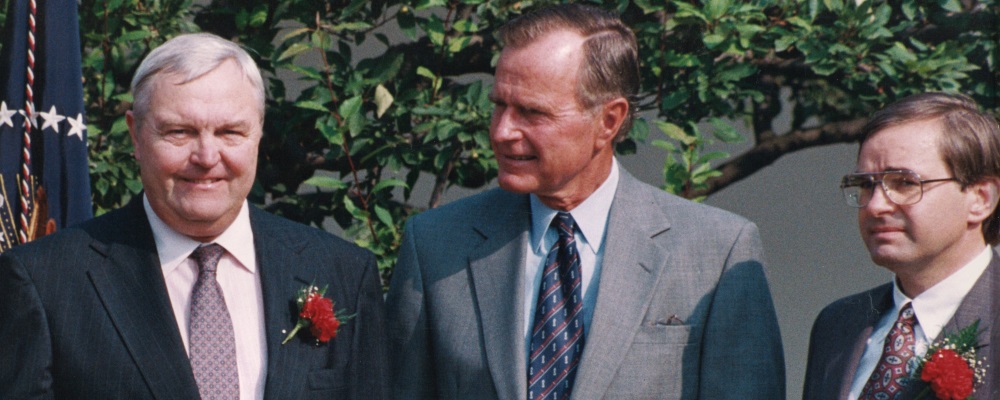
その他価格等自由記入欄
資料を請求していただいた方には、DFAソフトウェアの説明資料をお送りします。 また、ソフトウェアのデモやトライアルも可能です。 お気軽にお申し付けください。
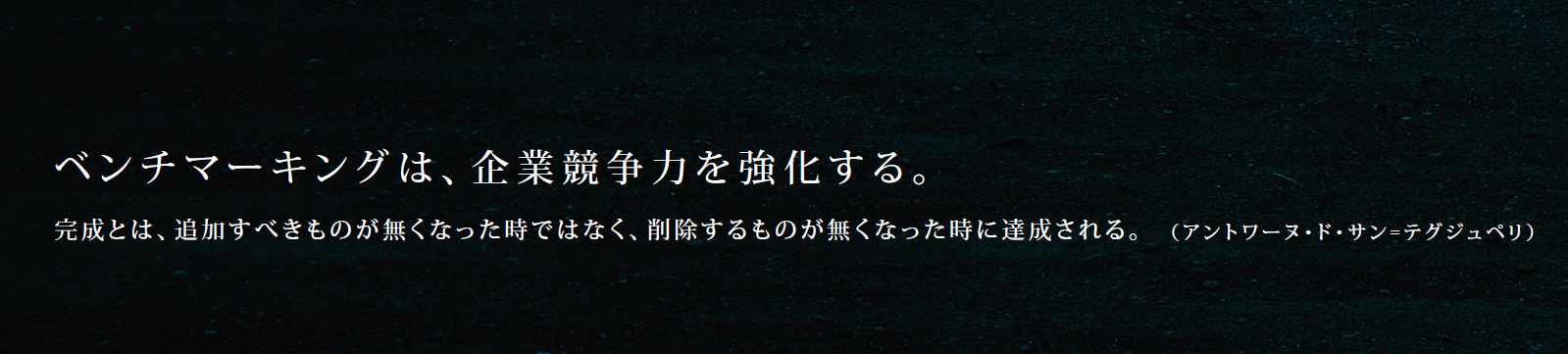