DFMA (部品数削減&製品コスト見積)2023 日本語版リリース
概要
1982年のリリース以来、世界で950ユーザに利用されてきたDFMAソフトウェアの V2023日本語版がリリースされました。 V2023では、DFMに新しく導入されたダイナミックコスティング分析と呼ばれる機能により、ユーザは入力項目をさらに簡略化することができます。
さらに実装済みの金属押出シミュレーション機能に加え、射出成形シミュレーション機能が追加されました。
DFMAはDFM(製品コスト見積)とDFA(部品数削減)モジュールから構成されています。
これは、DFA(組立のための設計)とDFM(製造のための設計)の間には互いに矛盾する要求が存在するからです。 製品設計の際は、シンプルで組立が容易な製品は、部品数が最少になるという考えを優先し、その後に生産工程を最も有効に活用できるように部品を設計すべきであるという考え方に基づいています。
この機会に、製品原価低減のためにDFMAの利用をご検討頂ければ幸いです。
さらに実装済みの金属押出シミュレーション機能に加え、射出成形シミュレーション機能が追加されました。
DFMAはDFM(製品コスト見積)とDFA(部品数削減)モジュールから構成されています。
これは、DFA(組立のための設計)とDFM(製造のための設計)の間には互いに矛盾する要求が存在するからです。 製品設計の際は、シンプルで組立が容易な製品は、部品数が最少になるという考えを優先し、その後に生産工程を最も有効に活用できるように部品を設計すべきであるという考え方に基づいています。
この機会に、製品原価低減のためにDFMAの利用をご検討頂ければ幸いです。
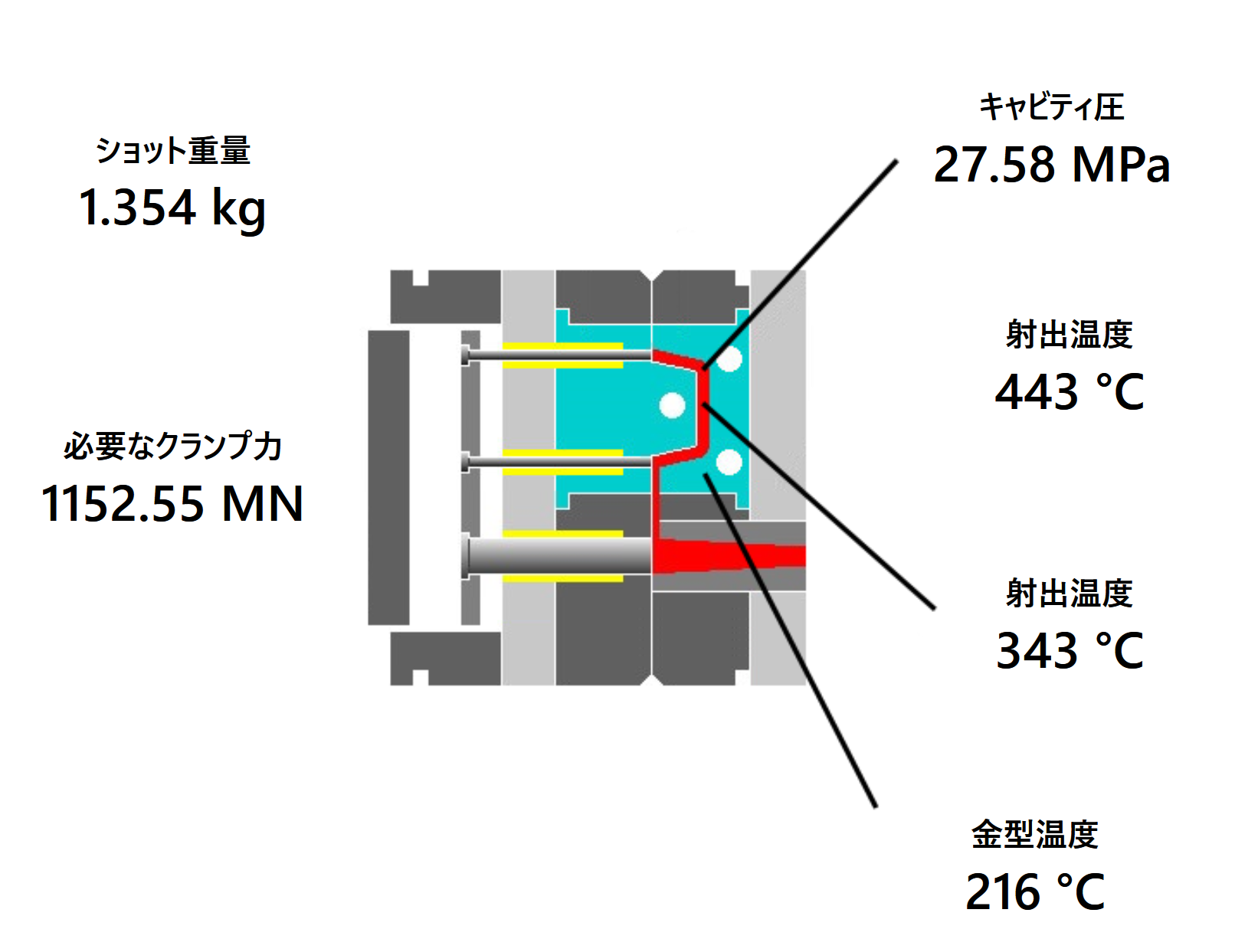
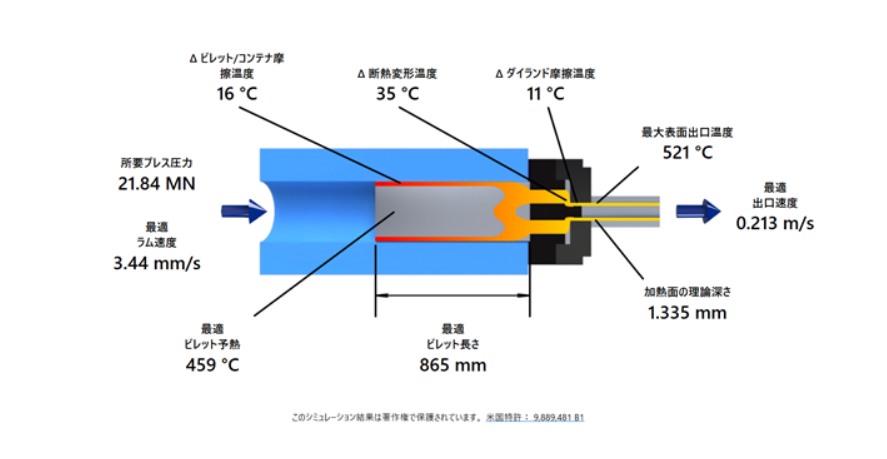
動画
特徴
今回のリリースでは、中国やインドなど世界中の加工機を含め、DFM機械ライブラリを刷新しました。
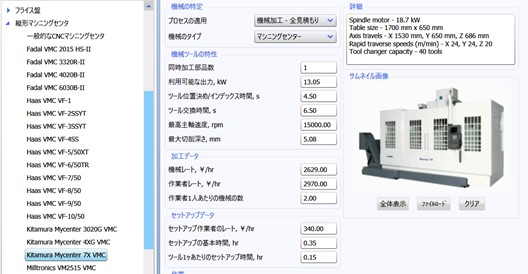
製品URL
用途・実績
DFMAはロードアイランド大学の2人の教授であるブースロイド博士とデュウハースト博士により開発された手法で「組立が容易な製品設計は部品数が最少になる」という考え方に基づいています。製造コストの8割は、設計の初期段階で決定されるといわれ、基本設計の段階で、様々な加工方法と異なる材料を使った製造コストを比較することにより、生産工程を最も有効に活用した部品を設計することができます。
DFMAは、学術的研究成果をもとに熟慮を重ねた製品コスト低減ツールです。その起源は1970年台の米国に遡ります。
DFMA - その背景
1970年代初頭、マサチューセッツ大学のGeoffrey Boothroyd教授とその同僚は、のちにDFMA®の基礎となる研究を始めました。当初その目標は、自動組立を容易にするために製品設計を定量化する手法を設計者に提供することでした。この手法はマニュアル組立にも拡大され、2つの基本原則が明らかにされました。
部品点数を減らすことにより組立作業の回数を低減する
組立作業を容易にする
この原則は、当時支配的であった「生産性ガイドライン」とはまったく対照的なものでした。当時の生産性ガイドラインは設計者に対し、個々の部品を簡素化するように指示していました。これにより部品の製造が容易になり、コストが削減されると考えたからです。 Boothroyd博士の画期的な研究は、個々の部品を簡素化するよりも、より少数の多機能部品を使用する方が大幅に製品コストが安くなることを明らかしたのです。
DFMA®ソフトウェア
この研究成果の商業的利用を検討するため、Peter Dewhurst博士が研究に加わり「自動、手動アセンブリの設計」(DFA)ソフトウェアが開発されました。 その後、IBMとDECの投資を受け、1983年、PC版ソフトウェアの開発のためにBoothroyd Dewhurst Inc. が設立されました。このDFAソフトウェアによりFordやGMなどの大手企業は数十億ドルのコストを節約したと言われています。
1985年、BoothroydとDewhurst博士は、さまざまな設計に対し設計初期段階で正確なコスト見積りを可能にする「Design for Manufacture」(DFM)モジュールを開発しました。 こうして、DFAとDFMの 2つのモジュールが組合わされ、現在DFMA®として知られているソフトウェアが完成しました。
現在
1991年、DFMAを開発した Boothroyd Dewhurst Inc は、米国の製造業の復権に貢献したとして、ブッシュ父大統領から、米国の技術者にとって最高の名誉とされる National Medal of Technologyを授賞しました。 Boothroyd Dewhurst Inc.は、30年以上にわたってDFMA®ソフトウェアツールの開発を続け、DFMA®ソフトウェアは、数百社の企業において低コストで高品質の製品製造を支援してきました。 そのBDI社のレガシーは、今日も引き継がれています。
DFMAは、学術的研究成果をもとに熟慮を重ねた製品コスト低減ツールです。その起源は1970年台の米国に遡ります。
DFMA - その背景
1970年代初頭、マサチューセッツ大学のGeoffrey Boothroyd教授とその同僚は、のちにDFMA®の基礎となる研究を始めました。当初その目標は、自動組立を容易にするために製品設計を定量化する手法を設計者に提供することでした。この手法はマニュアル組立にも拡大され、2つの基本原則が明らかにされました。
部品点数を減らすことにより組立作業の回数を低減する
組立作業を容易にする
この原則は、当時支配的であった「生産性ガイドライン」とはまったく対照的なものでした。当時の生産性ガイドラインは設計者に対し、個々の部品を簡素化するように指示していました。これにより部品の製造が容易になり、コストが削減されると考えたからです。 Boothroyd博士の画期的な研究は、個々の部品を簡素化するよりも、より少数の多機能部品を使用する方が大幅に製品コストが安くなることを明らかしたのです。
DFMA®ソフトウェア
この研究成果の商業的利用を検討するため、Peter Dewhurst博士が研究に加わり「自動、手動アセンブリの設計」(DFA)ソフトウェアが開発されました。 その後、IBMとDECの投資を受け、1983年、PC版ソフトウェアの開発のためにBoothroyd Dewhurst Inc. が設立されました。このDFAソフトウェアによりFordやGMなどの大手企業は数十億ドルのコストを節約したと言われています。
1985年、BoothroydとDewhurst博士は、さまざまな設計に対し設計初期段階で正確なコスト見積りを可能にする「Design for Manufacture」(DFM)モジュールを開発しました。 こうして、DFAとDFMの 2つのモジュールが組合わされ、現在DFMA®として知られているソフトウェアが完成しました。
現在
1991年、DFMAを開発した Boothroyd Dewhurst Inc は、米国の製造業の復権に貢献したとして、ブッシュ父大統領から、米国の技術者にとって最高の名誉とされる National Medal of Technologyを授賞しました。 Boothroyd Dewhurst Inc.は、30年以上にわたってDFMA®ソフトウェアツールの開発を続け、DFMA®ソフトウェアは、数百社の企業において低コストで高品質の製品製造を支援してきました。 そのBDI社のレガシーは、今日も引き継がれています。
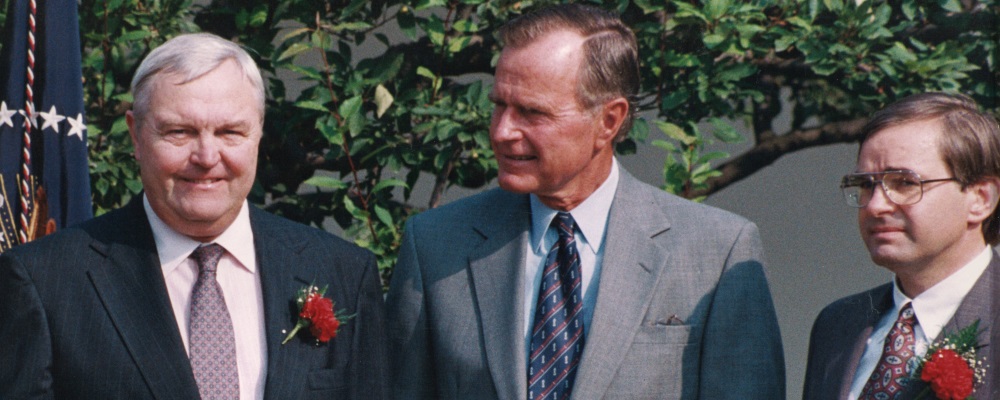
設備
DFMAは、強力なベンチマーキングツールでもあり、自社コスト低減のヒントを得るための競合製品のコスト解析を容易にします。 以下にDFMAを用いた競合製品のテアダウン手法をご紹介します。
DFMAによる競合製品のテアダウン手順:
1) 最初に、自社の製造工程で製品を組立てるのとは反対の分解順に、競合製品の部品をDFA(Design for Assembly)ソフトウェアの部品表に登録します。 各部品の組付方法を入力することにより製品組立時間と組立性を表すDFA指標が自動で計算されます。 (部材のコスト分析を行う場合にはこの手順は必要ありません)
2) 次に、DFAの部品表にある各部材に対しDFM(Design for Manufacture)によるコスト分析を行います。DFMソフトウェアには、各種の工程と材料に関するデータベースが組み込まれており、さまざまな材料と工法の製造コストを計算することができます。
コスト分析手法には3段階あると云われています。
• レベル 1 - 過去の経験や実績をもとに経験のある技術者の勘による見積。 類推による見積。
• レベル 2 - 類似の従来製品、予算、サプライヤの見積、経験者の意見、ある種の分析による見積。 パラメータ手法。
• レベル 3 – 材料費データベースと動作分析をもとに部品毎の詳細見積を行う。 サプライヤの見積や従来手法との比較において、高いレベルの精度を確保できる。 分析・エンジニアリング手法。
DFMAは、材料、機械、プロセスデータベースをコスト計算を行うDFMソフトウェアとは独立して設定することができ、正確なデータに基づくレベル3のコスト見積が可能です。 これらのデータベースには新規材料、機械、工程を登録することができます。
3) DFM分析により構成部品のコスト見積が完了したら、比較表により自社製品のコストと競合のコスト比較を行います。
4) DFMのレポート機能によりコスト要因を、材料費、セットアップ費、加工費、不良品費、金型費に横並び比較することができます。折れ線グラフは、異なる製法と材料により製品コストが総生産量に対してどのように変化するか示しています。
DFMAによる競合製品のテアダウン手順:
1) 最初に、自社の製造工程で製品を組立てるのとは反対の分解順に、競合製品の部品をDFA(Design for Assembly)ソフトウェアの部品表に登録します。 各部品の組付方法を入力することにより製品組立時間と組立性を表すDFA指標が自動で計算されます。 (部材のコスト分析を行う場合にはこの手順は必要ありません)
2) 次に、DFAの部品表にある各部材に対しDFM(Design for Manufacture)によるコスト分析を行います。DFMソフトウェアには、各種の工程と材料に関するデータベースが組み込まれており、さまざまな材料と工法の製造コストを計算することができます。
コスト分析手法には3段階あると云われています。
• レベル 1 - 過去の経験や実績をもとに経験のある技術者の勘による見積。 類推による見積。
• レベル 2 - 類似の従来製品、予算、サプライヤの見積、経験者の意見、ある種の分析による見積。 パラメータ手法。
• レベル 3 – 材料費データベースと動作分析をもとに部品毎の詳細見積を行う。 サプライヤの見積や従来手法との比較において、高いレベルの精度を確保できる。 分析・エンジニアリング手法。
DFMAは、材料、機械、プロセスデータベースをコスト計算を行うDFMソフトウェアとは独立して設定することができ、正確なデータに基づくレベル3のコスト見積が可能です。 これらのデータベースには新規材料、機械、工程を登録することができます。
3) DFM分析により構成部品のコスト見積が完了したら、比較表により自社製品のコストと競合のコスト比較を行います。
4) DFMのレポート機能によりコスト要因を、材料費、セットアップ費、加工費、不良品費、金型費に横並び比較することができます。折れ線グラフは、異なる製法と材料により製品コストが総生産量に対してどのように変化するか示しています。
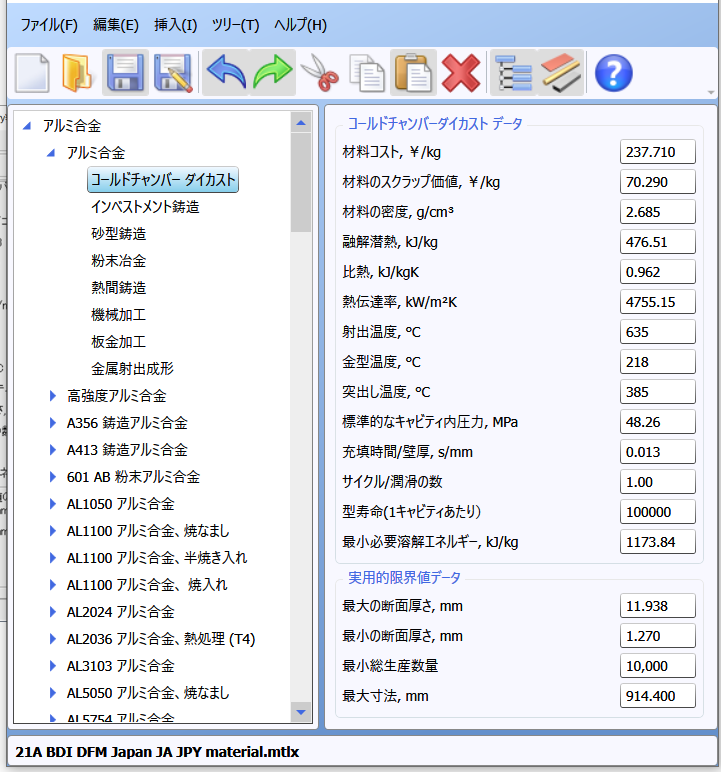
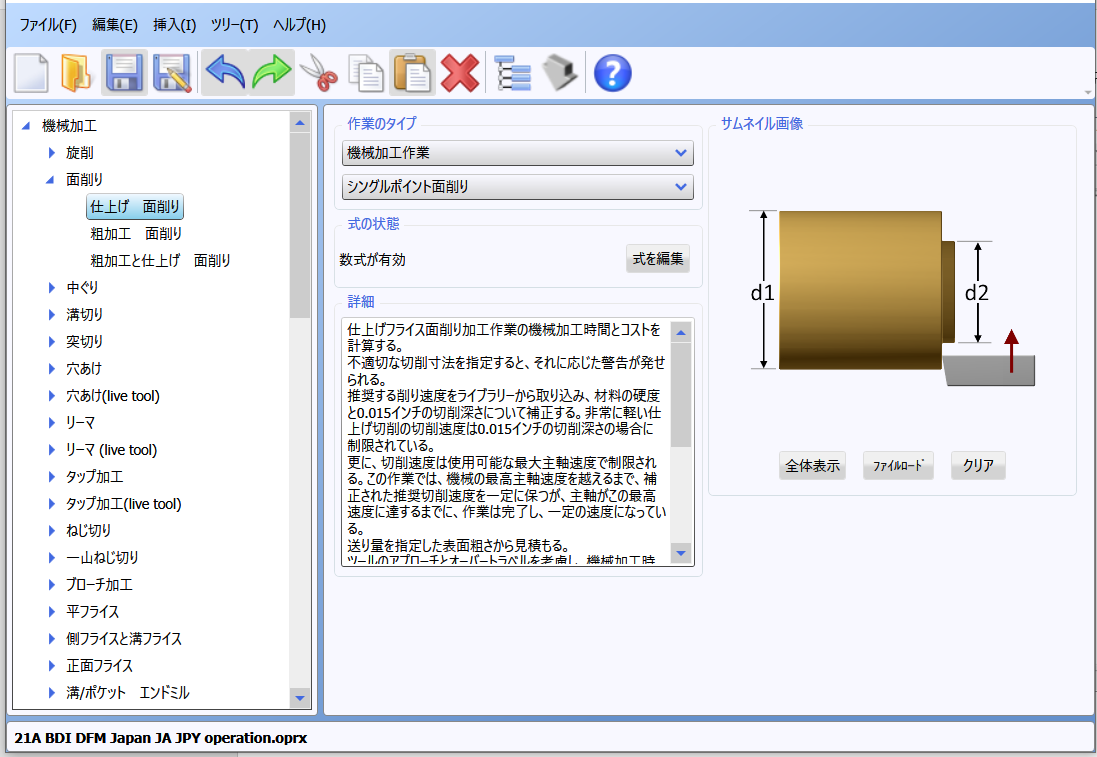
その他価格等自由記入欄
DFMAにより異なる材料、異なる工法、異なるサプライヤのレートをもとにコストシュミレーションを繰り返すことにより、設計の初期段階で、所定の製造数量に対して最も低いコストの製法と材料を客観的データに基づき選択することが可能になります。
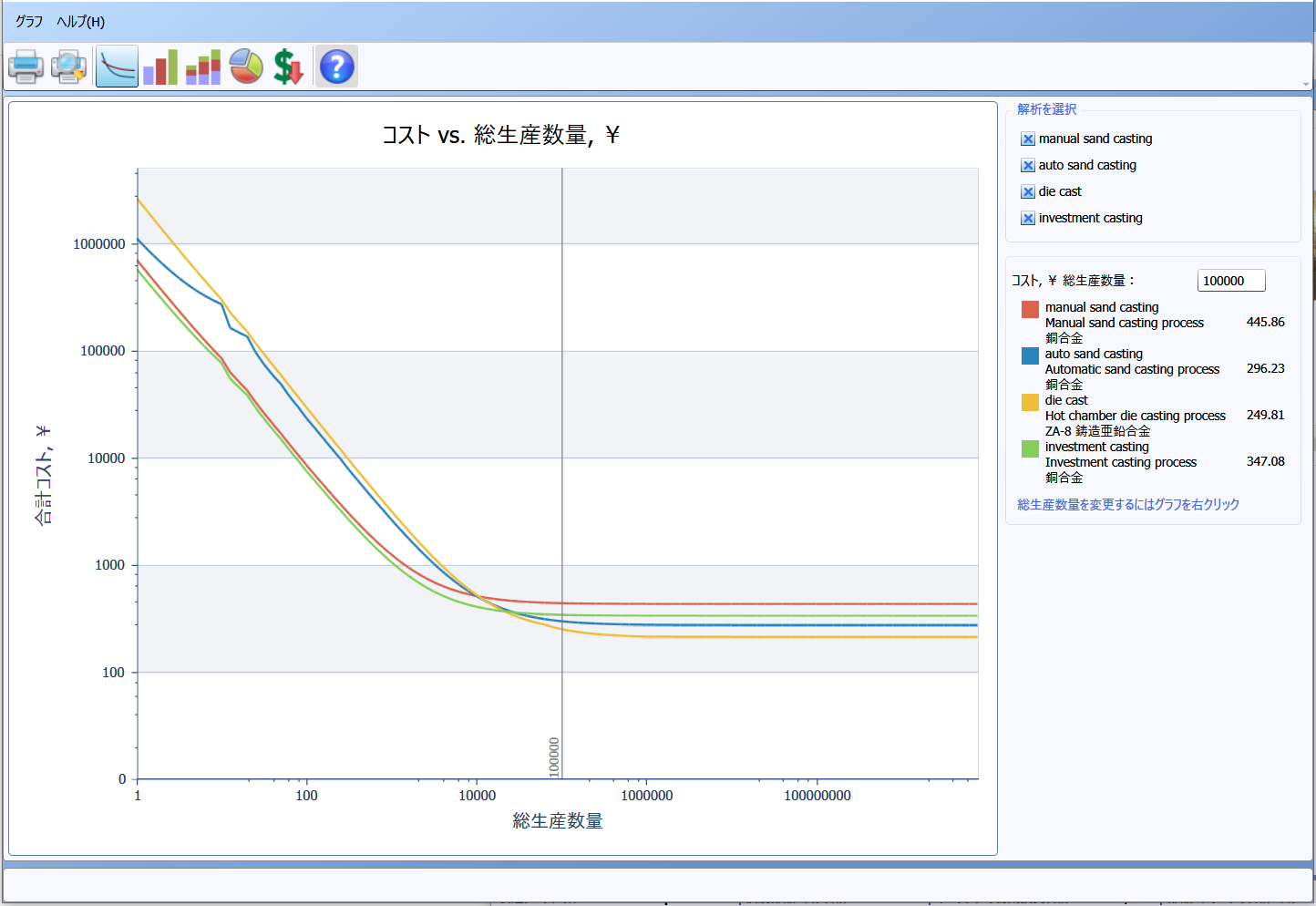
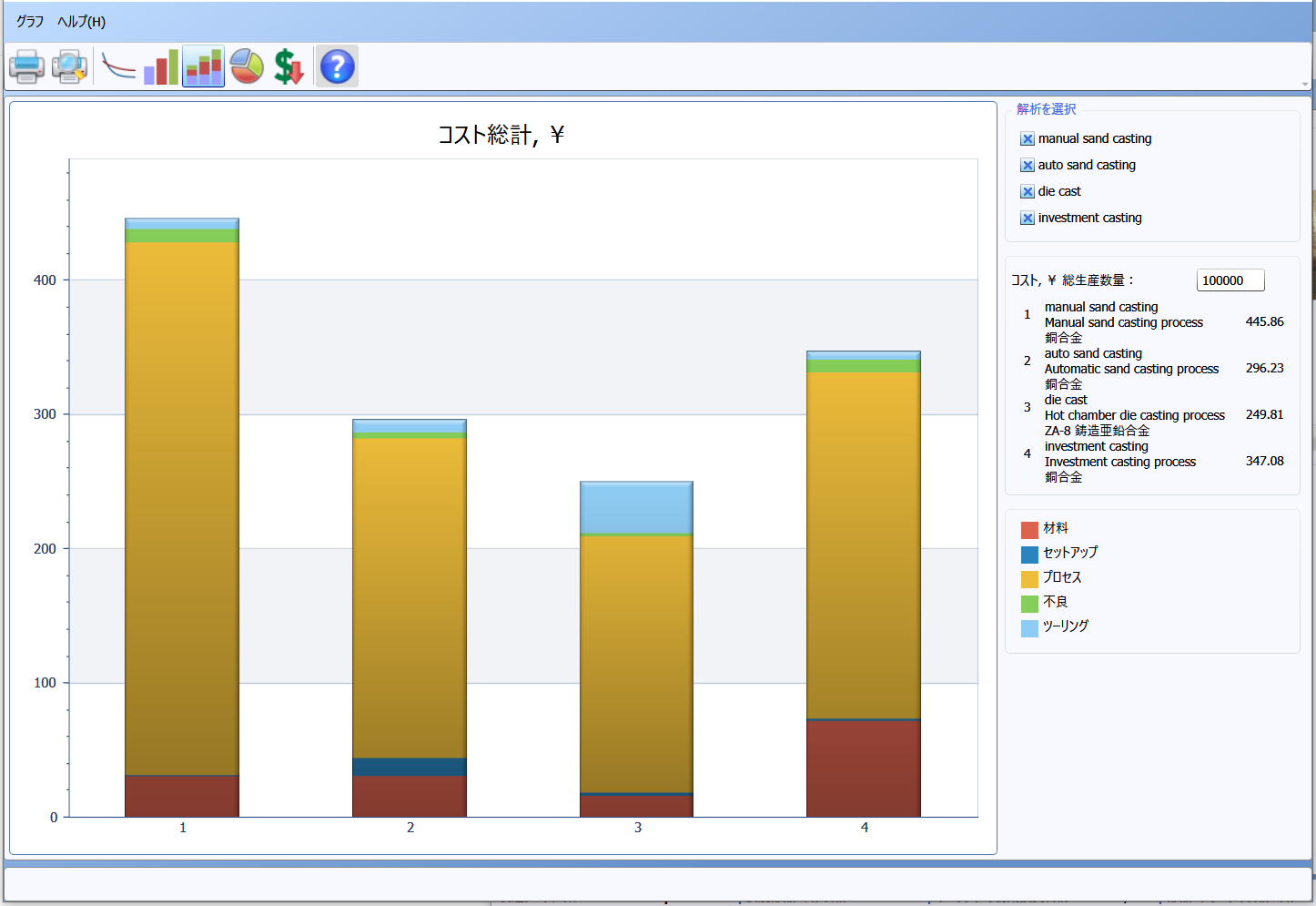