Archives of Past Exhibits:Riken
Tokyo Motor Show 2015
2015 JSAE Automotive Engineering Exposition
SiboDur iron alloy
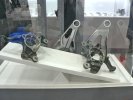
SHORIK quench-solidified aluminum powder alloy
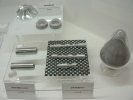
Cast iron parts (brake disc rotor)
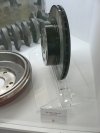
Cast iron parts (brake drum)
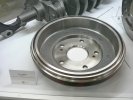
Piston ring
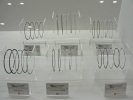
2014 JSAE Automotive Engineering Exposition
Tokyo Motor Show 2013
SiboDur - Iron alloy
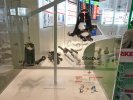
Seal ring
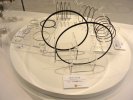
Tokyo Motor Show 2011
Tokyo Motor Show 2005
Tokyo Motor Show 2005
Piston ring
<Preventing Aluminum Adhesion Technology>
-"New Tough-RIK"
- Thermal resistance and wear resistance were improved thanks to the review of solid lubrication and improvement of binder made from thermal resistance resin.
<Surface Treatment Technology>
-DLC (Diamond-Like Carbon) / Amorphous Carbon
Engine parts
Deformed Hollow Tilt Camshafts
- Making shaft hole at the core along cam profile achieved weight reduction and less machining cost. Possible to make a hole of the oil-through-bore at one time.
Valve Lifter
- A combination of bonding techniques and downsizing allowed to reduce weight and to minimize engine size. A barrel shaped type reduced sound at the time of engine revolution and achieved to enhance the quietness. At the same time, less friction was achieved.
Aluminum Alloy Retainer
- Resistant to abrasion and achievement of weight reduction
Processed material parts
Double Wishbone Type Steering Knuckles
- Cost reduction by near-net-shape treatment of complex dimension. Reduced the
back-end process as well as realizing the easier-cutting. The unified component reduced
its weight.
Strut Type Knuckles
- The unified casting part of complex dimension.
Lower Control Arm
-Deletion of forged product and stamped product
Piston ring
<Preventing Aluminum Adhesion Technology>
-"New Tough-RIK"
- Thermal resistance and wear resistance were improved thanks to the review of solid lubrication and improvement of binder made from thermal resistance resin.
<Surface Treatment Technology>
-DLC (Diamond-Like Carbon) / Amorphous Carbon
application | material for cylinder | Features |
periphery | cast iron | less friction + better fuel consumption |
aluminum | preventing aluminum adhesion and scuffing + wear resistance + less friction | |
lateral | - | measure to abrasion of groove in the piston (preventing aluminum adhesion) |
Engine parts
Deformed Hollow Tilt Camshafts
- Making shaft hole at the core along cam profile achieved weight reduction and less machining cost. Possible to make a hole of the oil-through-bore at one time.
Valve Lifter
- A combination of bonding techniques and downsizing allowed to reduce weight and to minimize engine size. A barrel shaped type reduced sound at the time of engine revolution and achieved to enhance the quietness. At the same time, less friction was achieved.
Aluminum Alloy Retainer
- Resistant to abrasion and achievement of weight reduction
Processed material parts
Double Wishbone Type Steering Knuckles
- Cost reduction by near-net-shape treatment of complex dimension. Reduced the
back-end process as well as realizing the easier-cutting. The unified component reduced
its weight.
Strut Type Knuckles
- The unified casting part of complex dimension.
Lower Control Arm
-Deletion of forged product and stamped product